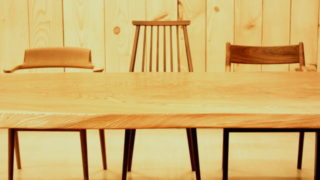
「一枚板ができるまで」の物語を紹介します。
少し長くなりますが興味のある方はご覧いただけたらと思います。
「一枚板ができるまで」と言って想像されるのは削ったり磨いたりなどの部分をまず思い浮かべられると思いますが、実はそこにたどりつくまでの方が時間と労力がかかるんですよ!
ここを理解していただけると価格に納得していただけると思います。
その一 良材の仕入れ
一枚板には良い材が不可欠です。日本全国の良材を求めて東へ西へ!!
材の仕入れは基本丸太です。大きなものは4t車に一本しか積めないこともあります。
その二 製材
最も重要な工程と言っても過言ではありません。
丸太の向きや鋸を入れる場所によって杢目や傷の出方が大きく変わるんです。
長年の経験で丸太の外見から内部を予測して決めるのですが「大当り」もあれば「大失敗」もあります。
その三 自然乾燥
製材したての材は大げさに言うとほとんどが水です。
作品をお届けした後に乾燥が進むと大変なことになるのでその前にしっかりと乾かします。
一枚板が曲がったり割れたりするトラブルは木の乾燥が進むときに起こるんですよ!
その「乾燥」の第一工程が「自然乾燥」になります。
長いものは10年以上! 板の間に桟を入れてゆっくりゆっくりと乾燥させます。
これにより良い色味を得たり材の暴れを抑えたりの効果があります。食べ物だと熟成させるようなものです。
長い時間とコストがかかる(お金をマイナス利息で置いてるようなもの)のでここを省略される業者さんもいらっしゃるようですが、
次の人工乾燥も含めてここを手抜きするとしっぺ返しが来ます。
その四 人工乾燥
当工房では「蒸気乾燥」というやり方です。温度と湿度を調整して水分を抜いていくのですが簡単に言えば約70℃の部屋のなかに約一ヶ月入れて乾燥させます。エアコンがない時代はここまでする必要はありませんでしたが急な温度湿度変化があるエアコン下では必要不可欠な工程です。乾燥後には含水率(高周波を使った計測器があります)をチェックします。
残念ながらこの工程で大きな割れが入り作品として使用できなくなる材(小物雑貨で活用します)もあります。
厳しい条件を耐え抜いた材だけが一枚板として作品になることを許されるんですよ!!
その五 木取り
その材ができるだけ活きるように「形」「サイズ」「杢目」などを考えておおまかチェンソーでカットします。
余談ですができるだけいい材で作りたいので誰がその材をとるかは社長を含めてみんなでじゃんけんです。
その六 平面に削る
乾燥した板は曲がったり反ったりしています。これを平面に削ります。
夢を壊すようで申し訳ないですがこの工程はカンナではなく機械です、手作業でもできますが少しでも価格を抑えるための企業努力です。
その七 形を整える
切りっぱなしの木口や自然だけど使い勝手に影響する部分などを手作業で形を整えます。
できるだけ素材を活かすように、自然の形と違和感がないように仕上げていきます。
その八 磨く!磨く!磨く!
ここも夢を壊して申し訳ありませんがカンナ仕上げではありません。ベルトサンダー→手作業でピカピカに光るまで磨きます。
おもて面だけでなく普段見えないうら面もほぼ同じように仕上げます。美しい塗装をするためにはここが重要です。
いくら塗装の技術があっても磨きの技術と妥協しない根気がなければ良い仕上がりにはなりません。
その九 塗装
塗装にはウレタン仕上げを採用しています。以前はオイル仕上げや漆も手がけたこともありますが
ほとんどメンテナンスフリーのウレタンに再仕上げを希望されるお客様も多く現在ではほぼ100%ウレタンで仕上げています。
ご希望であればオイル仕上げも可能です。
その十 最終チェック
磨き残しや塗装のムラなどがないか細かくチェックします。
一品ものかつ展示現品販売なので残念ながらお客様が車のキーや指輪などでキズをつけられるケースもまれにあります。
お買い上げいただいた後にもう一度キズなどがないかさらに細かくチェック後にお届けします。